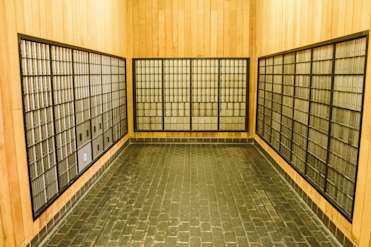
Starting your own business
Alternatives to a PO box address for your small business
Simple, smart accounting software - no commitment, cancel anytime
FINANCE, BUDGETS AND CASHFLOW
Accounting plays an essential role in manufacturing, with multiple costs to keep track of throughout the manufacturing process. It’s like accounting on Nightmare Mode!
From raw materials to finished goods, here’s a basic guide to principles of accounting in the manufacturing industry – plus how QuickBooks accounting software can make it easier.
Accounting is never an afterthought in manufacturing – you have to track costs throughout the production process, from transferring finished products to operating machinery.
By optimising efficiency and evaluating company profits at every stage, it can make the difference between your business running out of money, or driving sustainable growth.
Accounting in manufacturing is defined by its intricate management of overhead costs, materials and employee labour. There are specialised costing methods, such as job order, process and activity-based costing, alongside different ways of tracking inventory.
It sounds complex, but once you understand the principles, it becomes easier to understand.
Manufacturing accounting is tailored to calculate all the costs involved with manufacturing business – such as running a factory, moving raw materials or products, and paying workers.
Below are some principles to help calculate the full expense or Total Manufacturing Cost.
Some expenses can be traced directly to producing specific goods, such as buying raw materials or the direct labour involved in manufacturing the product. Direct costs can be split into direct materials (often listed in a bill of materials) and direct labour (such as payroll).
Indirect manufacturing costs, also known as manufacturing overhead, cover costs that can’t be traced directly to the product. These can include rent, utilities or maintenance costs.
The Cost of Goods Sold and the Cost of Goods Manufactured are two important principles in manufacturing accounting. They help differentiate between costs related to all the goods manufactured and sold in a time period, versus costs for inventory created but not yet sold.
Tracking these helps analyse production costs and the total profit in a financial period.
Fixed manufacturing costs are constant, regardless of how many products are made in a time period – they include things like monthly rent and the salaries of permanent employees.
Variable costs depend on the volume of production, such as electricity or raw materials.
Manufacturing costs include a wide variety of components throughout the production process. Including the below can give a comprehensive view of the expenses involved.
Raw materials – costs for the materials used for products, such as timber
Labour costs – costs for paying your employees for their physical labour
Factory overheads – indirect costs, such as heating or renting a factory
Accounting in manufacturing uses three types of costing methods. These can be used for different manufacturing situations – such as for consistent production or one-off projects.
Suitable for unique or custom-made products
Costs are tracked for specific jobs or orders
More time-consuming as gives more details
Example: A furniture company creates bespoke furniture for custom orders. The raw materials and labour needed would be different for each piece, needing a unique cost.
Used in continuous production processes
Costs are an average from multiple products
Fast and efficient method for identical items
Example: A bakery produces thousands of identical loaves of bread. In process costing, an average cost would be calculated for the flour, overheads and labour for a standard loaf.
For allocating costs based on activities
Useful for assigning indirect costs to products
Ideal for factories with diverse overheads
Example: A car manufacturer produces various models of cars on the same production line. Activity-based costing would identify activities like welding or painting. For example, the activity-based cost of painting a car would include costs for paint and employee labour.
Costs in manufacturing companies can be complex, but getting to grips with basic principles of accounting helps make it easier. But what else is important in manufacturing accounting?
Another important accounting principle for manufacturing operations is reliable inventory management. It’s crucial for businesses to ensure the best allocation of resources, minimise carrying costs, and ensure accurate tracking of expenses – ultimately leading to profit.
Inventory is the value of your manufactured items, and they’re split into various stages:
Raw materials – the basic components needed to create your product, such as flour and yeast for bread, wood and glue for furniture, or metal and paint for cars
Work-in-progress – WIP inventory includes unfinished items in the middle of production, alongside the costs associated with turning raw materials into goods
Finished goods – fully completed products that are ready for sale or transport, which represent potential revenue for the business and the culmination of efforts
Knowing your product inventory can give a more accurate picture of your financial health.
There are also different methods of managing your inventory and therefore your accounting. Each of these calculation methods have their pros and cons, depending on your business.
In FIFO, the oldest items in your inventory are sold first
This can be useful for items with a shelf life, such as food
If inventory costs are rising, this can result in higher profits
It can also mean the balance is overstated and more tax
The opposite of FIFO, LIFO means the newest products are sold first. It’s ideal for companies that want a lower net income and lower taxes, but may not work as well for perishables.
Common method for companies with identical items
Calculates an average cost across multiple products
Ideal for when cost per item is difficult to estimate
The COGS is divided by the total number of products
The opposite of average costs, this method requires meticulous bookkeeping. It will be unsuitable for fast-selling goods but can be ideal for bespoke items like jewellery.
As you can see from the above, there are many different ways to record your costs.
Now you know some manufacturing accounting terms and principles, here’s how you can use QuickBooks to help with the complex process of bookkeeping for manufacturing.
Unsure whether QuickBooks is right for your manufacturing business? Give us a call!
With QuickBooks, you can track costs across the whole of your manufacturing business. From expenses like raw materials and factory overheads to paying your labourers.
Track profitability and impress investors with cutting-edge reporting. Keep an eye on your cash flow and get a true picture of your financial performance to make better decisions.
QuickBooks is recognised by HMRC for Making Tax Digital for VAT, making meeting tax deadlines easier. Our industry know-how helps you to comply with VAT rules.
Automate payroll, invoicing and more with an innovative suite of accounting tools for manufacturers. From production forecasts to tracking inventory, we’ve got you covered.
Whether you’re a small business that creates bespoke items, to a manufacturing company creating thousands of products per day, QuickBooks can grow with your business needs.
Lastly, here are a few tips for manufacturing businesses during the accounting process.
Keep an eye on your inventory – too much can cost you money, while not having enough can put you out of business. Software can help alert you to imbalances.
Think about external market factors, such as fluctuating shipping or raw material costs. This is particularly important when you’re trading goods internationally.
Don’t underestimate your factory overhead costs. Heating for your workers, electricity for machinery, it all adds up. Accounting software can help you see the big picture.
Use the right costing and inventory methods for your business – a company making unique, time-consuming products will have different needs to a commercial factory.
Avoid inventory discrepancies by regularly making records of products. Software can help streamline inventory tracking, for example by using barcodes or serial numbers.
Now that you’ve read our top tips for manufacturing accounting, give us a call to see which of our software packages is right for your manufacturing business size and requirements.
The information on this website is provided free of charge and is intended to be helpful to a wide range of businesses. Because of its general nature the information cannot be taken as comprehensive and they do not constitute and should never be used as a substitute for legal, accounting, tax or professional advice. We cannot guarantee that the information applies to the individual circumstances of your business. Despite our best efforts it is possible that some information may be out of date. Any reliance you place on information found on this site or linked to on other websites will be at your own risk.
9.00am - 5.30pm Monday - Thursday
9.00am - 4.30pm Friday