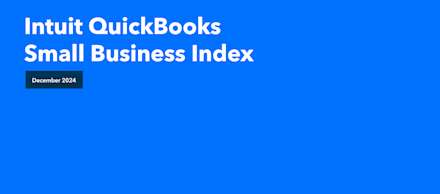
Intuit QuickBooks Small Business Index, December 2024
Simple, smart accounting software - no commitment, cancel anytime
Weeks on Hand is an essential metric for understanding how long you can sustain your business operations based on inventory levels. All businesses that sell products need to work out their Weeks on Hand inventory regularly to prepare for potential stock-outs and protect revenue.
Use our free calculator to calculate your Weeks on Hand automatically and assess your inventory levels regularly. Or you can view the Weeks on Hand formula if you want to work it out manually.
Using our free Weeks on Hand inventory calculator is straightforward. Simply gather your average weekly usage and inventory levels. Then, input your figures into our calculator, and you’ll have your inventory’s Weeks on Hand.
Weeks on Hand is a metric that measures the number of weeks a company can sustain its operations based on its current inventory levels. It estimates how long the existing inventory can meet the demand before you need to make more.
For instance, if a company has 10,000 units of inventory and the average weekly usage is 1000 units, the Weeks on Hand is ten weeks (10,000 units / 1000 units per week). Based on the average usage rate, the existing inventory can support operations for around ten weeks before you need to manufacture additional inventory.
Weeks on Hand is a useful metric for inventory management. It helps businesses determine how adequate their current inventory levels are, plan for production, manage capital, and make effective decisions about stock replenishment to meet customer demand without facing stock-outs or excess inventory.
Read more: managing inventory as an online business.
The Weeks on Hand formula is:
Weeks on Hand = (Current Inventory Level / Average Weekly Usage)
You need to gather two key pieces of information:
Average Weekly Usage: Work out the average amount of inventory you use or sell weekly. Calculate by dividing the total inventory usage or sales over a specific period by the number of weeks.
Inventory Level: Determine the current inventory level. This is the quantity of inventory available at a given point in time.
Once you have these figures, you can start calculating your Weeks on Hand using the formula.
Need a hand? Here's a step-by-step guide for calculating Weeks on Hand inventory:
Determine the average weekly usage by choosing a specific period for which you want to calculate Weeks on Hand (e.g., a month or a quarter) and determine the total inventory usage (or sales) for that period. Divide the total inventory usage by the number of weeks in that period to calculate the average weekly usage.
Determine the current inventory level by taking a physical count or reviewing your inventory records to determine the current inventory quantity available.
Calculate Weeks on Hand by dividing the current inventory level by the average weekly usage calculated in Step 1. The result of this calculation represents the number of weeks the current inventory will last depending on the average weekly usage rate.
Let’s look at an example.
You want to calculate Weeks on Hand for a specific product. During a quarter (13 weeks), the total units sold were 500. So, the average weekly usage is 500 units / 13 weeks = 38.46 units per week.
If the current inventory level for that product is 500 units, the calculation would be as follows:
Weeks on Hand = 500 units / 38.46 units per week ≈ 13 weeks
Weeks on Hand is an essential metric for determining whether you have enough inventory to meet customer demand, allowing you to plan and adjust your production schedules.
QuickBooks provides reports offering insights into your sales. By running sales reports or customising reports based on inventory usage, you can gather data on the number of items sold or used within a specific period.
To use our powerful software, sign up for QuickBooks today or start your 30-day free trial.
Weeks on Hand focuses on the duration your inventory can sustain operations based on your current inventory level and current average weekly usage. It looks backward in time.
On the other hand, weeks of supply focuses on the estimated time it will take to exhaust your inventory based on the current inventory level and future average weekly demand. It looks forward in time.
The frequency you should calculate Weeks on Hand depends on your type of business and the demand volatility.
In some industries, calculating Weeks on Hand inventory every month may be adequate. Others may require more frequent calculations, such as daily or weekly, especially if demand and inventory turnover are high. It's important to balance monitoring inventory levels regularly and not getting overwhelmed by too many calculations.
Seasonality can significantly impact weeks of hand calculations. During peak seasons or periods of high demand, Weeks on Hand may decrease as inventory is bought and sold rapidly. During slower seasons or periods of low demand, Weeks on Hand may increase as inventory usage decreases.
It's essential to account for seasonality when analysing your Weeks on Hand values to ensure accurate inventory planning and management. This is where weeks of supply can also come in handy.
This content is for information purposes only and should not be considered legal, accounting or tax advice, or a substitute for obtaining professional advice specific to your business. Additional information and exceptions may apply. Applicable laws may vary by region, state or locality. No assurance is given that the information is comprehensive in its coverage or that it is suitable in dealing with a customer’s particular situation. Intuit does not have any responsibility for updating or revising any information presented herein. Accordingly, the information provided should not be relied upon as a substitute for independent research. Intuit does not warrant that the material contained herein will continue to be accurate nor that it is completely free of errors when published. Readers should verify statements before relying on them.
We may occasionally provide third-party links as a convenience and for informational purposes only. Intuit does not endorse or approve the views or opinions of any corporation or organisation or individual herein. Intuit accepts no responsibility for the accuracy, or legality, of third-party content.
9.00am - 5.30pm Monday - Thursday
9.00am - 4.30pm Friday