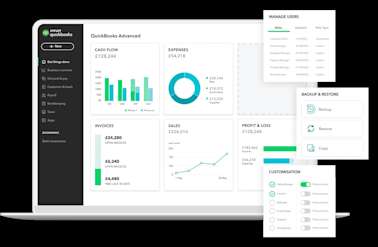
Cloud accounting
Accountant and bookkeeper product update - Your Books is now "Advanced"
Smart accounting software - no commitment, cancel anytime
Business owners have a lot to worry about, from accounting to marketing and operations. In business, there is never enough time. A long lead time can have detrimental effects on your business if you miscalculate your safety stock levels.
This can be made worse if you face a reorder delay, or even worse - a supply delay. You will also need to factor in manufacturing lead time if you order finished products.
Calculate lead time quickly and easily using the calculator below.
In inventory management, lead time is the amount of time between when you place an order and when it is received.
If you manage lead time well, you can reduce wastage and downtime, avoid holding costs, and maximise your profits. If you do not track lead time, you will likely see major issues in your processes, whether it's a lack of raw material for a development process or finished stock for your shelves. Calculating lead time is also an important part of project management.
There are many different factors that go into how lead time is calculated. Lead time can be affected by factors beyond your control like distance, customs processing time, etc. Since these factors are outside your control, you can only complete your lead time calculations to efficiently manage your safety stock and inventory turnover.
The lead time formula is simple:
Lead time = Supply delay + reorder delay
Step one is to factor in the reordering delay. For example, if your supplier accepts orders once a week, and you placed the order four days before they will accept it, you’ll have to factor that into your cycle time. That four days is a reordering delay. The supply delay is how many days it takes for a fulfilled order, which means when the order is in your possession.
Use the above lead time calculator to quickly determine the amount of time between placing your order and receiving it.
Lead time impacts your total inventory levels, and the longer the lead time, the more holding stock you will need. A longer lead time makes your deliveries unpredictable, which means you are heavily reliant on accurate demand forecasts.
Once you have accurate figures for your supply and reorder delays, you can input these numbers into the lead time calculator to calculate your lead time.
Inventory management software can do an excellent job handling the heavy lifting for you. With QuickBooks, you will be able to track your inventory to get real-time stock value, low stock alerts and many more features.
Visit our pricing page to get a 30-day free trial.
Yes, there are. There are material, factory, production, customer, and cumulative lead times. You can learn the production lead time by adding the customer, material, and factory lead times together.
There are a variety of factors that determine a lead time in inventory management. You’ll have to consider:
Preprocessing
Processing
Waiting
Storage
Transportation
Inspection
You can categorise these factors into three stages. The preprocessing stage is the before, the processing stage is during, and the shipping stage is after.
Lead time is the time between a business placing a customer order and the business receiving the order. It's a key component in order management, and many businesses seek new ways to reduce lead time.
This content is for information purposes only and should not be considered legal, accounting or tax advice, or a substitute for obtaining professional advice specific to your business. Additional information and exceptions may apply. Applicable laws may vary by region, state or locality. No assurance is given that the information is comprehensive in its coverage or that it is suitable in dealing with a customer’s particular situation. Intuit does not have any responsibility for updating or revising any information presented herein. Accordingly, the information provided should not be relied upon as a substitute for independent research. Intuit does not warrant that the material contained herein will continue to be accurate nor that it is completely free of errors when published. Readers should verify statements before relying on them.
We may occasionally provide third-party links as a convenience and for informational purposes only. Intuit does not endorse or approve the views or opinions of any corporation or organisation or individual herein. Intuit accepts no responsibility for the accuracy, or legality, of third-party content.
9.00am - 5.30pm Monday - Thursday
9.00am - 4.30pm Friday