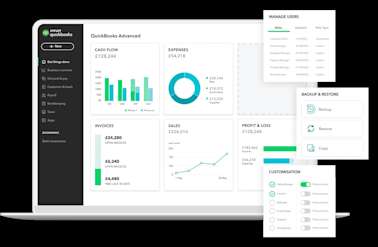
Cloud accounting
Accountant and bookkeeper product update - Your Books is now "Advanced"
Smart accounting software - no commitment, cancel anytime
Work In Process (WIP) inventory, also called Work In Process inventory, is crucial for creating an accurate balance sheet, as it represents the value of goods at all stages of the manufacturing process before completion. Using this guide and our Work In Process calculator, you can quickly and effectively work out your WIP inventory.
Using our Work In Process calculator will automate your calculations. You simply need to input your beginning WIP inventory, manufacturing costs, and your completion percentage. After adding these to the calculator, you’ll receive your WIP inventory number.
WIP inventories are goods or products in the intermediate stages of the production process. It represents the value of materials, labour, and overhead costs that you’ve already spent but haven’t finished transforming into the end product.
In manufacturing and production, products will likely go through several stages before reaching the final finished goods stage. WIP inventory includes partly finished items that are being actively worked on or are awaiting more processing. This inventory category exists between raw materials inventory and finished goods inventory.
WIP inventory is crucial for businesses that engage in production or manufacturing, as it represents the investment in the production process.
Here is a general formula for calculating your Work In Process inventory.
WIP Inventory = Beginning WIP Inventory + Manufacturing Costs - Cost of Goods Completed
If you use the first-in, first-out (FIFO) accounting method, you must assign costs depending on the order in which materials or units are added to production. Use the following formula:
WIP Inventory = Cost of Beginning WIP Inventory + Cost of Units Started or Transferred In - Cost of Completed Units
Calculating Work In Process inventory is straightforward. You must determine the value of your partially finished goods in the manufacturing line. The method you need to use varies depending on your business’s accounting system.
Here is a basic WIP calculation:
Identify the direct costs of the production process. These costs typically include direct materials, direct labour, and manufacturing overheads.
Determine the equivalent production units for each cost component. Equivalent units represent the partially completed units in terms of fully completed units. This step involves accounting for the completion percentage for each cost component.
Allocate the direct costs to the equivalent production units. For each cost component, like direct materials, direct labour, and manufacturing overhead, you must multiply the cost per unit by the equivalent units for that component.
Add up the costs of each component to calculate the total cost of the WIP inventory. This total represents the value of partially completed goods in your production line.
The specific formulas and calculations may differ depending on the accounting method your company uses, such as the weighted average method or the FIFO method. Ensure you double-check your accounting process before using this step-by-step guide.
Accurately calculating WIP inventory allows businesses to report their financial position and reflect on the value of inventory at various stages of completion. Using QuickBooks Online expense management software, businesses can record and track the costs of their WIP inventory by entering direct material costs, direct labour costs, and manufacturing overhead costs.
Ready to automate your WIP inventory calculations? Sign-up for QuickBooks today or start your 30-day free trial and take control of your inventory management.
WIP inventory ties up cash flow as it represents costs incurred in the production process that is made back through sales. Effectively managing WIP inventory and minimising excess WIP levels can help improve cash flow by reducing tied-up capital and improving production efficiency.
WIP inventory helps businesses monitor and control production costs. By tracking the value of partially completed goods, businesses can identify cost overruns, inefficiencies, or bottlenecks in the production process. This information enables business owners to make informed decisions and improve operational efficiency, reduce waste, and control operational costs.
WIP inventory represents goods still undergoing production or processing. These goods have incurred some costs but are not ready for sale or use. In contrast, finished goods inventory are goods that are ready for sale.
This content is for information purposes only and should not be considered legal, accounting or tax advice, or a substitute for obtaining professional advice specific to your business. Additional information and exceptions may apply. Applicable laws may vary by region, state or locality. No assurance is given that the information is comprehensive in its coverage or that it is suitable in dealing with a customer’s particular situation. Intuit does not have any responsibility for updating or revising any information presented herein. Accordingly, the information provided should not be relied upon as a substitute for independent research. Intuit does not warrant that the material contained herein will continue to be accurate nor that it is completely free of errors when published. Readers should verify statements before relying on them.
We may occasionally provide third-party links as a convenience and for informational purposes only. Intuit does not endorse or approve the views or opinions of any corporation or organisation or individual herein. Intuit accepts no responsibility for the accuracy, or legality, of third-party content.
9.00am - 5.30pm Monday - Thursday
9.00am - 4.30pm Friday