If your clients make products, you may need to help them with cost accounting, and there are a few different types of numbers you should track. These include standard, actual, and budgeted costs. Depending on the situation, you may want to use all of these costs in different ways. Here’s a closer look at how these concepts work and a few tips on how to utilize them.
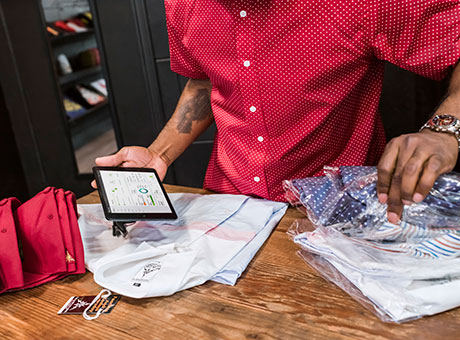
What Types of Costs: Actual, Budgeted, or Standard?
What Are Standard Costs?
In cost accounting, standard costs refer to the usual costs incurred in production. If your client has been in business for a while, it should use historic numbers to assess standard costs, and as long as these numbers are consistent, it can decide whether it wants to include direct costs or both direct and indirect costs. Direct costs such as materials are directly related to production, while indirect costs refer to expenses such as labour and overhead.
How About Actual Costs?
As implied by the name, these are the actual costs incurred during production. Actual costs can vary from standard costs due to changes in the prices of materials, differences in employee productivity, shifts in scale, and multiple other reasons. To explain, imagine the standard cost of creating 1,000 widgets is $10,000 or $10 per widget, but when the company creates 80 widgets, the actual cost ends up being $1,000 or $12.50 per widget. That difference may be due to the change in the scale of production.
In some cases, crises or mistakes can affect actual costs. For instance, say a company calculates its standard costs for producing a batch of gizmos, but then an employee makes a huge error in the production process requiring the company to scrap those materials and start over, thus increasing the actual production costs. Crises ranging from natural disasters to broken machinery can all lead to variances between standard and actual costs.
And Then…Budgeted Costs?
Budgeted costs tend to overlap with standard costs, but they’re not exactly the same. In many cases, companies take the standard costs from the previous year and use them as their budgeted costs for the current year. Alternatively, businesses can use standard costs as a jumping off point to set their budgeted costs. In many situations, companies break down standard costs per unit, but they use budgeted costs for overall expenses. You can determine the best way to utilize these numbers for your clients.
Using all These Different Costs Together
Whether your clients are creating a budget or trying to identify the most effective production methods, standard costs provide a useful data point. For example, if a client is trying to create a budget and knows prices are going up, it can add the projected increase in materials to the standard price to create the budgeted amount.
Your client can also look for variances between actual and standard costs to identify where to make changes. In fact, these comparisons are so useful that many companies track the numbers side by side for instant results. Imagine a company is expecting to pay $1,000 as the standard cost for a certain material but when it actually buys the material, it only pays $900. If it sees that difference immediately, it knows its profits are likely to be higher than usual. Similarly, if a company uses $20,000 as a standard figure for monthly labour expenses but then incurs $25,000 in payroll costs, the accounting records immediately note that 25% increase. This acts as a red flag so the company knows it needs to make some labour changes.
Production costing is tricky, but it’s essential in manufacturing. If a company wants to be able to create budgets, forecast cash flows, or keep expenses consistent, it needs these numbers. Explain these types of costing methods to your clients and let them know which ones they should track and use.