Managing inventory is an essential part of your small business, especially if you are in the manufacturing or sales industries. One way to determine when you should order more inventory items is to calculate a reorder point. Knowing how to do it can save you time and money.
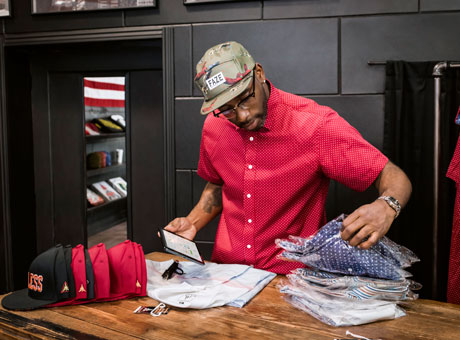
What Is a Reorder Point?
What is a Reorder Point?
What is a reorder point? A reorder point tells you when to purchase a specific amount of an inventory item to replenish your stock. The reorder point is at the unit level of your small business inventory, and it’s a crucial measurement in your inventory management system.
This point represents the inventory level at which it’s most efficient for you to submit an inventory order to your supplier. When you calculate the inventory reorder point accurately and use it correctly, you eliminate the risk of interrupting your production or fulfillment activities.
At the same time, you’re minimizing the amount of inventory in stock and maintaining good cash flow. When you reach the reorder point, although your inventory is low, you have enough inventory on hand to meet your customer demand while your supplier fills and delivers your new order.
How a Reorder Point System Helps Your Small Business
If you manufacture or sell goods, the reorder point is vital for your small business success. Using the reorder point system minimizes the cost of maintaining inventory because it takes your typical order quantity into account. By calculating the reorder level, you know the most efficient level of inventory to purchase at a particular time.
Keeping track of this point, or using reorder point quantity alerts in your inventory management system, allows you to keep your ordering and shipping costs low. You’re ordering in enough time to avoid extra expenses for rush deliveries, and you’re satisfying your customers’ needs with the inventory you have on hand, which means your cash flow stays steady.
How to Calculate the Reorder Point
To make accurate calculations, the reorder point model requires that you know your average daily sales, the lead time for delivery, and your safety stock level. Perhaps you sell bottles of ABC liquid laundry detergent at your store. Here’s the equation for calculating your reorder point for the detergent:
Reorder Point = Average Daily Sales x Lead Time + Safety Stock
- Average Daily Sales is the average of your sales over time. If you sell 5 bottles of detergent per day Monday through Thursday (20 bottles) 10 bottles each on Friday and Saturday (20 bottles), and nine bottles on Sunday (nine bottles) your total sales for the week is 49 bottles. Your average daily sales figure is seven bottles (20 + 20 + 9 = 49 bottles divided by 7 days = an average sale of seven bottles per day).
- Lead Time is the time span between placing your inventory order with your supplier and receiving it. Your lead time depends on factors such as whether the items are available, the transportation method, weather delays, and the distance it has to travel to your location. If you order 150 bottles of detergent on a Monday morning in May and your order arrives by truck on Thursday morning, your lead time is four days. However, in December, your lead time might be 6 days due to a snowstorm, poor driving conditions, and shipment delays due to the holidays. So you might decide to use an average lead time, five days, in your calculation.
- Safety Stock is excess inventory that’s a buffer between your sales forecast and your actual sales. Keeping safety stock in your inventory ensures you have enough units on hand if your customer demand increases, someone breaks, spills, or steals items, or you need to fill unexpected orders. With safety stock, your business can still fulfill orders while you’re waiting on more inventory arrivals. You might want to set your safety stock figure as your maximum daily sales (10 bottles) minus your average daily sales (seven bottles) for a daily safety stock figure of three bottles per lead time day.
In this example, your reorder point calculation looks like this:
7 Bottles x 5 Days + (3 bottles x 5 days) = 50 Bottles
When your inventory of ABC liquid detergent reaches 50 bottles, you are at the reorder point. If you order 150 bottles, that gives you enough for three weeks worth of sales (49 bottles per week). While you wait for your order, which may take four to six days, you have seven days worth of inventory on hand (49 bottles), ready to sell. You’re prepared for continuing sales, satisfying customers, and keeping your cash flow going.
Managing, ordering, and tracking inventory efficiently helps you keep customers happy and boosts your bottom line profits. Having the right tools simplifies your responsibility. 5.6 million customers use QuickBooks. Join them today for free to help your business thrive.