Inventory management is the process by which inventory is ordered, organized, counted, sold and accounted for. The management of inventory and stock is essential to any business based on selling goods, and part of that is knowing the methods and terms for such things. Familiarizing yourself with these inventory terms will help you with the management of your goods.
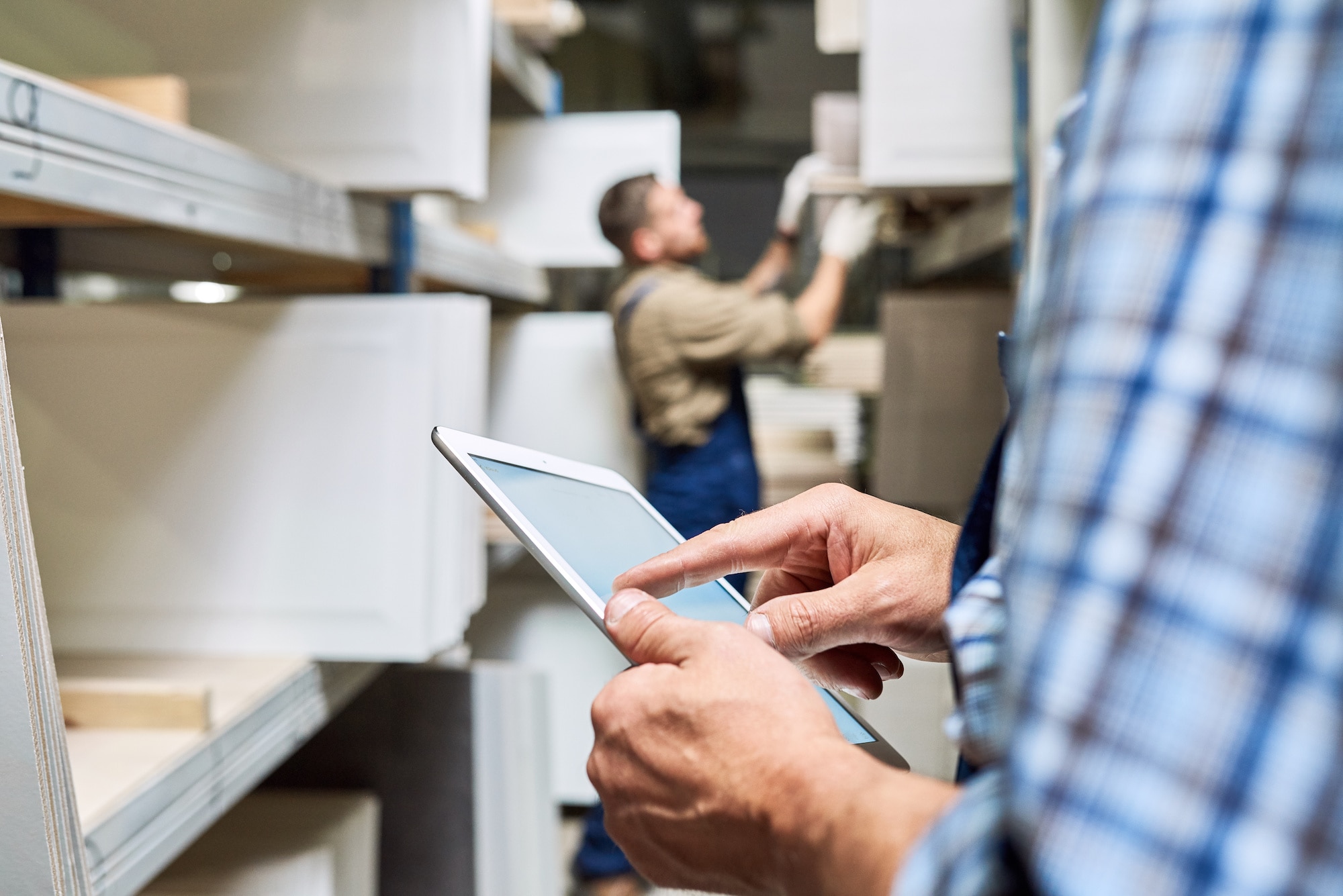
21 Most Common Inventory Terms
Common Inventory Concepts
As a business owner you will want to have as tight a grasp on your inventory as possible. These various concepts can help you with supply chain management, warehouse management as well as inventory management and enterprise resource planning. Listed below are 21 of the most common terms used when discussing a business’s inventory system.
1. Inventory control
Inventory control, also known as stock control, is the act of looking over and ensuring the business’s inventory is up to date and in possession of the appropriate goods. Controlling inventory means verifying that popular products are in stock while cutting down on slow-selling goods.
2. Stocktake policies
Stocktaking is the process of counting and recording the number of products within a stock or inventory. Stocktaking policies refer to the procedures to deal with the supply and merchandise in a specific way. Every business will have their policies that act as guidelines for the way employees manage the stock.
3. Purchasing procedure
A purchasing procedure is a process by which a business chooses to buy their inventory. Companies will have a trigger in place that when an inventory item reaches a specific number, the company will automatically buy more of that item to restock their shelves. This is typically completed with inventory software that helps business owners manage their stock easier.
4. Stock-out management
Stock-out refers to the unexpected demand for specific inventory items, causing them to sell out, making them no longer available or in-stock at the store. Stock-out management is handling these events and planning of inventory to prepare for and stop stock-outs from happening.
5. Deadstock management
Goods that do not sell are considered deadstock inventory. A business will try and manage low-selling inventory before it becomes deadstock, as wasted inventory losses money.
Deadstock management is the process of managing unsold inventory before it becomes too problematic for the company. Inventory management software can help a business eliminate this stock from the inventory before it becomes obsolete, mitigating the losses to revenue in the process.
6. Age management
Aged inventory refers to the items in stock that have spent an unusually long period of time on the shelves compared to other products. Age management is the overseeing of aged inventory, dealing with these items in a smart way as not to lose money.
Throwing out aged products is the equivalent of throwing money straight into the trash. Managing aged inventory means finding a solution for these items, such as a bulk sale or discount, where customers can buy multiple items before they go out-of-date and become deadstock.
7. Carrying cost
Carrying cost refers to the total amount of expenses associated with the storing of unsold inventory. Typically, a business’s carrying cost will total twenty to thirty percent of its entire inventory costs of a calendar year. Successful inventory management can reduce that number with stock control and tracking for quicker turnaround of goods.
This cost is always depicted as a percentage of the total value of a business’s inventory. To calculate the carrying cost, divide the total inventory value by the cost of storing the goods over a specific period, multiplied by 100.
Carrying cost (%) = (Inventory Storage Costs / Total Inventory Value) x 100
To complete this formula, your business will first need to know the inventory storage costs, which are made up of four main components: capital cost, inventory service cost, inventory risk cost, and storage space cost. Add these four costs together to find out the total inventory storage costs, then continue with the formula to find the percentage of your business’s inventory carrying costs.
8. Warehouse stock
Warehouse stock, or warehouse inventory, refers to the entire inventory, including products, finished goods, raw materials, and work-in-process goods, owned by a business for resale. A warehouse is considered a building outside of the facility that a company uses to enact transactions, it is separate from the storefront.
9. Batch picking
Batch picking describes the method of collecting identical orders for your inventory at the same time. Instead of filling one order at a time, batch picking allows a business to complete numerous orders that are similar, all at once, for faster order fulfilment.
10. Cycle counting
Cycle counting is a part of inventory auditing, which takes a small sample of stock and cross-references it with the business’s financial and inventory records to make sure everything matches up.
Cycle counting is a sampling technique that provides companies with a quick snapshot of their inventory status using one category or section of stock to reflect the state of the whole inventory.
There are three main types of cycle counts that a business can use on their inventory, these include:
- Control Group Cycle Counting: This method focuses on repeat counting of the same items in a small time frame to uncover any inconsistencies in the counting technique.
- Random Sample Cycle Counting: This method counts a random selection of a certain number of inventory items each cycle count to ensure proper stock management.
- ABC Cycle Counting: This cycle count uses the ABC inventory management technique, which groups various stock items into groups A, B, and C, based on value. In this case, A would cover the most expensive items and is the category that is counted more frequently than the others.
11. Costing method
A costing method is a systematic approach to assessing the value of an inventory. There are three main types of costing methods that do this for a business’s stock. These are:
- FIFO Method: First in, first-out method whereby the oldest items are recorded as sold first and are expensed, but are not necessarily physically sold at that time.
- LIFO Method: Last in, first-out method whereby the cost of the most recently acquired items is the first to be expensed.
- Weighted Average Method: The weighted average cost per unit can be found by dividing the value of the goods available for sale by the number of units still in stock.
Inventory valuation and costing methods will directly impact a business’s financial statements and, therefore, an essential aspect of the inventory management process.
12. Lead time
Lead time refers to the time delay of inventory in transit. The lapse of time it takes to place a purchase order with the supplier to its delivery to the business is considered the lead time. The lead time directly impacts the amount of stock a company has at any point in time and should account for ordering and supply delays.
With this in mind, a company should always have enough safety stock on hand to cover demand during the lead time of deliveries.
13. Gross margin
The gross margin is the percentage of sales revenue a business retains after covering the costs associated with its production. This percentage is the company’s net sales revenue minus the cost of goods sold. Businesses aim for a higher percentage, as it means they retain more capital to be reinvested in the company. To determine this margin, the formula is as follows:
Gross Margin = Net Sales – Cost of Goods Sold
14. Initial mark-up
The initial mark-up refers to the amount of money a business will add to the goods for resale after they have been purchased from suppliers. This figure is expressed as a percentage of the initial cost of the purchased goods.
For example, a store owner buys furniture from the manufacturer for $400 a piece and sells them for $800 each. The furniture’s initial mark-up is %100. The purpose of this mark up is to allow companies to generate profit beyond what they paid for the item in order to make a living.
15. Velocity reports
A velocity report helps companies make important inventory decisions for purchasing and reordering stock. The report measures the business’s speed in which they sell their inventory items, what they have on hand currently, and how many units they should order in the future.
Companies can reference their velocity reports the next time they place a sales order or blanket order for goods to ensure the amount fits appropriately within their inventory system.
16. Sell-through
Simply put, sell-through rate is a sales metric that helps businesses to monitor the flow of their supply chain. It is shown as a percentage and illustrates the amount of inventory a business has sold within a month versus the amount of inventory shipped to them by a supplier.
17. Reorder points
A reorder point is when inventory levels dip below a certain point and trigger the reordering of those goods. Businesses will need to determine the minimum amount of stock they need on hand before triggering the reorder point and purchasing further goods.
18. Order hold time
The order hold time is the amount of time a business will wait before beginning the order fulfillment process. Holding orders creates a delay in the shipping process which allows businesses to ensure all orders are correct before being sent out. Using an order hold time companies can control costs and decrease mistakes.
19. Pick and pack
Pick and pack refers to the order fulfillment process. Creating an efficient pick and pack process can help businesses cut down on overhead costs while improving efficiency. There are four steps included in this process:
- Order Receiving: A customer places an order that the warehouse receives and generates a packing slip for their orders.
- Order Picking: Employees find the ordered items in the warehouse and pick them out per order.
- Order Packing: The picked items are then packed and made ready to be shipped out.
- Order Shipping: The orders are sorted by carrier and sent out to the loading dock ready to be shipped out.
20. Ending inventory
At the end of an accounting period or fiscal year, businesses must account for their stock, known as ending inventory. The ending inventory figure will be used in your financial statements to calculate the cost of goods sold (COGS) in that accounting period. It will directly affect your inventory budget for the next period.
Conversely, the state of a business’s inventory at the beginning of an accounting period is known as the starting inventory and should be recorded on the financial statements.
To determine the COGS for a period, you will need to add the starting inventory with the purchases of goods made, minus the ending stock.
The final figure will illustrate how much inventory you have sold within that time period. Overall, ending inventory and COGS is an essential aspect of your business’s profit and loss statements and should be calculated and looked over with care.
21. Inventory turnover
For a business to determine how much inventory they sold in a given period, they will use the inventory turnover ratio to illustrate the number of times the company has sold and replaced their stock. The inventory turnover formula is as follows,
Average Inventory = (Beginning Inventory + Ending Inventory) / 2
By calculating inventory turnover, businesses can learn how fast they sell inventory compared to the industry average to help measure their performance. Depending on the industry standard, a low or high ratio is preferred.
Software Can Help Better Manage Your Inventory
Many of these methods and techniques in dealing with stock inventory can be improved and expanded on using the right software for your management system. QuickBooks Online provides businesses with inventory tracking features on top of the extensive and comprehensive accounting and business management capabilities.
Next time you need to calculate COGS, check inventory transactions, find out the inventory on hand, check sales orders or quantity of an item, complete a cycle count, or implement a costing method, then QuickBooks Online can help. Know your inventory inside and out with the inventory tracking software. Try it free today and improve your return on inventory investment!