Understanding the workflow of inventory, whether producing the final product yourself or using suppliers to do it, can help with business management and inventory accounting. This guide will help you learn about the costs associated with WIP inventory, including what it is and how to manage it.
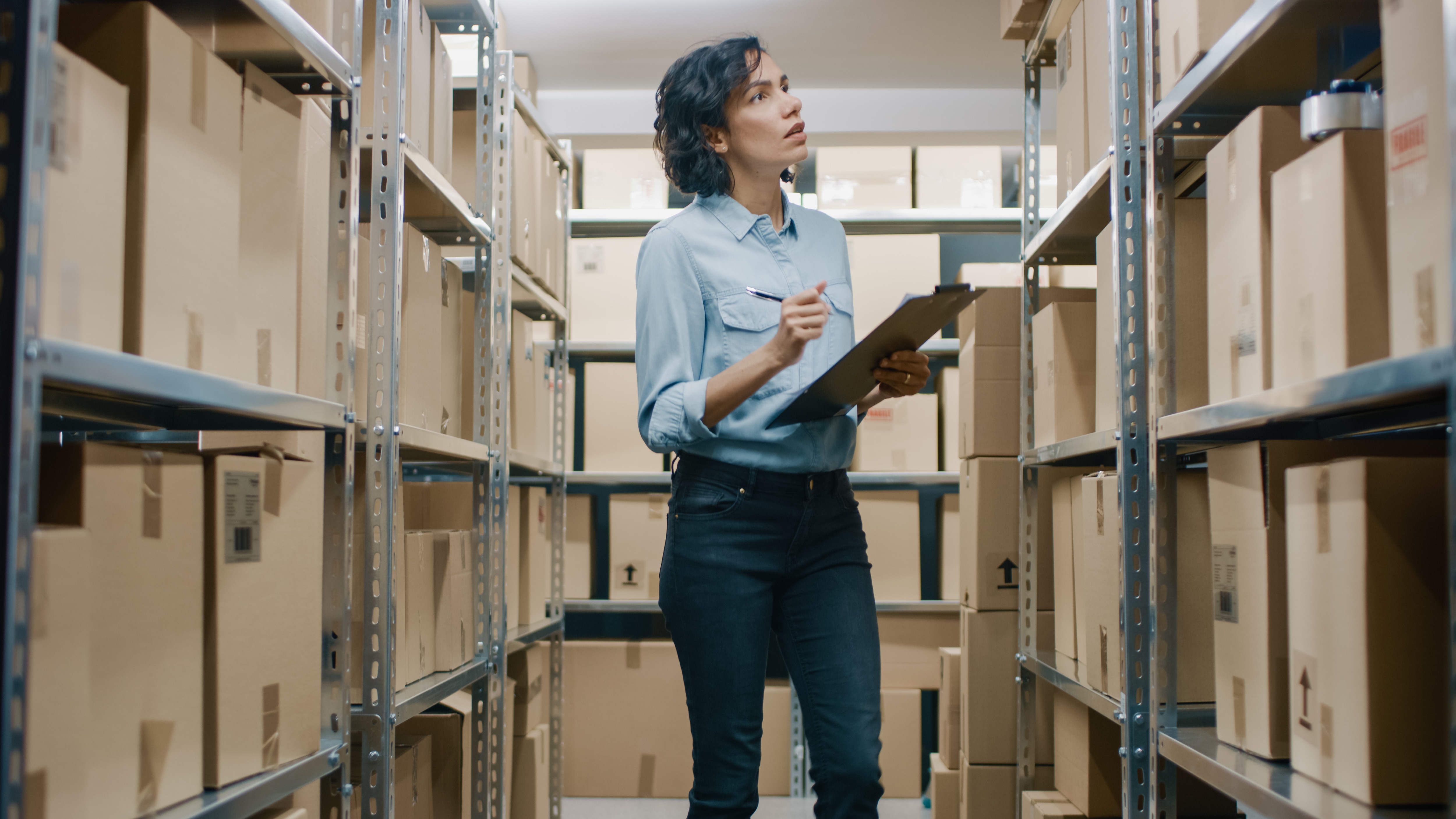
Work in Process Inventory Guide
What is Work in Process Inventory?
Work in process (WIP) refers to the partially finished goods in the middle of the manufacturing process. Work-in-process inventory is the stock of these partially completed materials before they are used to create a finished product. WIP is part of supply chain management.
Once the work in process inventory has gone through the production process, it will be considered your business’s finished goods inventory.
Work in process vs work in progress inventory
Many people use work in process inventory interchangeably with work in progress inventory, pinning it down semantics. However, there is a distinction between the two when it comes to this concept in the accounting and manufacturing industries. Typically, work in process is considered inventory, covering raw materials and the like, while work in progress is assets, on a larger scale.
Common Work in Process Inventory Terms
Small business owners and managers should familiarize themselves with common inventory terms to ensure good management practices. These are the terms that are directly related to work in process inventories and the manufacturing process:
- Beginning work in process inventory: The beginning WIP inventory is the previous accounting period’s ending WIP inventory, meaning it is the number of materials currently owned by the business to be used in the production process.
- Ending work in process inventory: The ending WIP inventory is the number of materials currently owned by the company at the end of the accounting period. This ending figure is used for the beginning inventory WIP of the next period.
- Cost of manufactured goods: Also known as COGM, this refers to the costs of purchasing or production of the products that a business sells within each accounting period.
- Manufacturing costs: Refers to the total cost of manufacturing within a given period. It is the sum of all costs associated with direct materials, direct labour, and overhead.
Calculating Work in Process Inventory
To calculate your business’s WIP inventory accurately, you will need to know the work in process inventory formula. Understanding the terms listed above is key to this process.
The WIP formula:
Ending WIP Inventory = Beginning WIP Inventory + Manufacturing Costs – COGM
Using this WIP formula, businesses can calculate how much work in process inventory they will have left over at the end of the accounting period. Once the period is over and the figure is calculated, this number becomes the beginning work in process inventory for the new period.
Tips for Improving WIP Inventory Workflow
Turning raw materials into your finished goods inventory can be a straightforward, yet fragile process. A business must account for labour and overhead costs, raw materials inventory, cost of raw materials, and the finished goods on the company’s balance sheet, while also ensuring the process of turning the materials into finished products runs smoothly.
To improve your business’s inventory management of work in process goods, consider implementing these tips below.
Use just in time manufacturing (JIT)
This method of production management dictates that materials are only acquired and used in the manufacturing process when the product is accounted for or sold. By using just-in-time manufacturing, companies can reduce waste overall while upping turnover to lessen the amount of cash tied up in these materials.
Identify bottlenecks to prevent backup
Any backup that occurs in the production process is known as a bottleneck. A delay at different stages of the supply chain and turning raw materials into finished goods can prolong the work process. This, in turn, takes greater means to fix, such as increasing direct labour or expenses such as overhead costs. By ensuring that each manufacturing stage runs smoothly, you can offset the chances of a costly bottleneck.
Keep organized and up to date on training
Since inventory is its own beast in business management, an organized inventory system can do wonders for keeping everything under control. This includes keeping all employees up to date on the latest inventory processes and procedures to ensure orderly and steady production.
Your whole workforce should understand each stage of the manufacturing process, including WIP inventory, to keep the operation running smoothly. Having a thorough onboarding process also helps new hires become familiar with everything to keep production going without issue.
Work with transparent suppliers
For businesses that do not have much control over work-in-process inventory, the focus should be on sourcing the right suppliers. Whatever manufacturer your company works with should be transparent about their processes. Using a quality supplier means being able to ask them about the raw materials used, information on production lead times, and whether or not the goods could be produced closer to home.
Use the right tools
Businesses of all sizes and inventory types can look to software to help them manage their products. For help with your inventory needs, try using QuickBooks Online inventory management and accounting software. With inventory tracking, cash flow planning, small businesses can keep an expert eye on their finances when dealing with inventory and manufacturing costs. Start your free trial today.