Inventory shrinkage refers to the difference between the physical count of your stock and the amount your records say you should have.
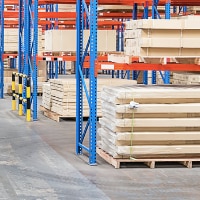
6 strategies to reduce inventory shrinkage
Unlike dead stock, which refers to stock that’s sitting on shelves and unlikely ever to be sold, inventory shrinkage is any loss of inventory that isn’t due to stock being sold. Some of the biggest culprits of inventory shrinkage are theft, damage to stock, and mismanagement of inventory.
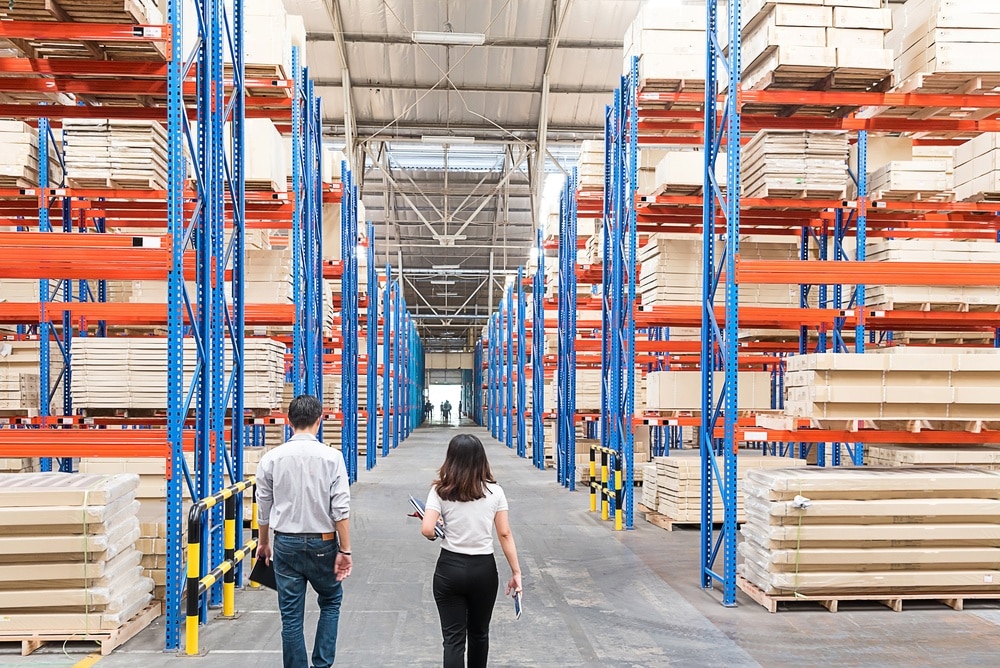
Inventory shrinkage can create major problems for businesses because it can result in a loss of sales and profits. In fact, the 2016 National Security Survey found that inventory shrinkage costs businesses a whopping $45.2 billion in 2015. Loss of inventory also makes it difficult to measure the number of times inventory is sold or used in a defined period, also known as inventory turnover.
However, the good news is that inventory shrinkage can be greatly reduced by putting some simple processes in place.
Implement a double-check system
One of the most straightforward ways to prevent inaccuracies in inventory management and stocktake is to have more than one person do a check when accepting inventory, signing off on invoices, etc. Introducing a system of double checks is also a good way to pinpoint and rectify any stages in the inventory management process where mistakes are occurring.
Give products unique identities
Proper products SKUs and UPCs are crucial in ensuring your recorded stock levels are correct and to reduce inventory shrinkage.
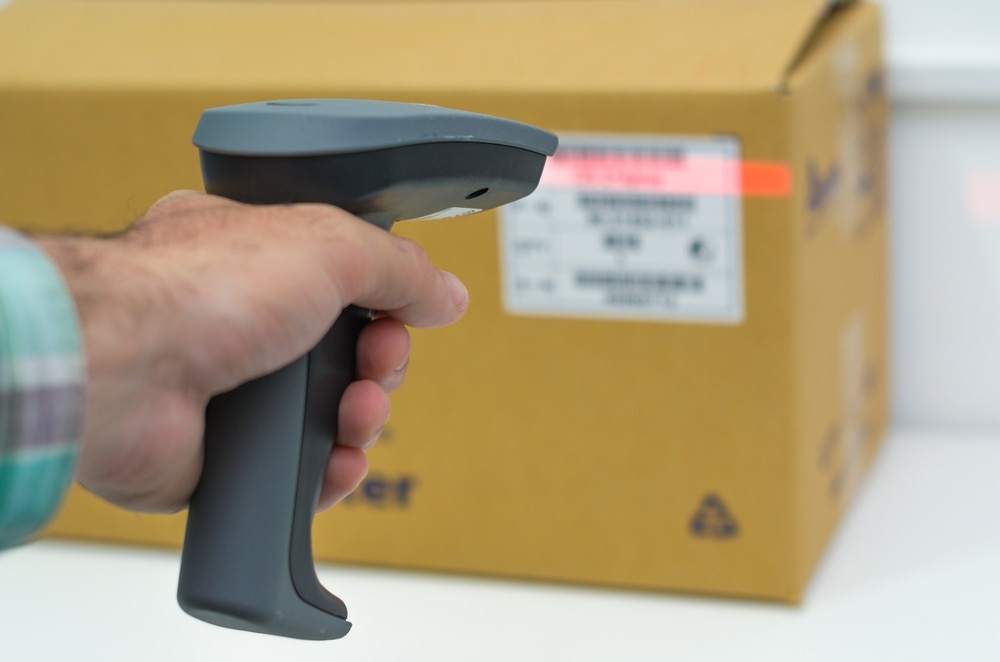
Make sure your product codes are as clear and simple as possible, and part of a system that can easily be expanded to accommodate new products. Use our free SKU generator to help you implement SKU best practices.
Conduct employee vetting and training
35.8% of inventory shrinkage is due to employee theft, which means it’s critical to properly screen candidates. Depending on your business, you may want to ask for employee references and do a background check before hiring. It’s also important to have training procedures in place, so that staff members know how to handle inventory properly and count stock.
Automate inventory management with software
The reality is that many inaccuracies in stock levels are due to human error. By streamlining and organizing your stock using a dedicatedinventory management software, you can reduce manual handling and processing of stock, and cut down on inventory shrinkage due to administrative mistakes.
Plan for busy periods
It can be especially difficult to accurately count and record stock during busy periods when demand is higher, staff are under pressure, and returns and exchanges tend to increase. Making sure you’re adequately prepared for peak sales periods ahead of time means you’ll have the proper systems in place to continue to manage inventory levels efficiently when demand increases.
Track inventory shrinkage over time
Each time you do a physical inventory count, compare the totals with your recorded inventory levels and calculate your percentage of inventory shrinkage. Ideally, this number will decrease over time as you refine your inventory management techniques. If the percentage of inventory shrinkage increases, it’s time to examine why this might be happening and circle back to the techniques above to ensure you have proper monitors and controls in place.
Streamline your inventory management processes and reduce inventory shrinkage by starting a free 14-day trial of TradeGecko’s stock control software.