Stock replenishment is one of the most important considerations when it comes to inventory management, as it helps ensure the right stock is on the shelves at the right time, while keeping inventory holding costs low and customers happy.
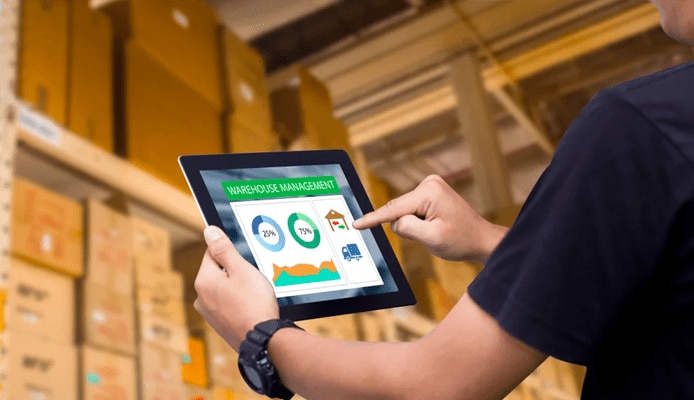
What is Stock replenishment?
What is stock replenishment?
Stock replenishment is the rate at which inventory travels along the supply chain from the manufacturer to the supplier to warehousing, picking, and shipment locations. The aim of stock replenishment is to keep inventory flowing through the supply chain at an optimal rate by maintaining efficient order and line item fill rates. This process helps prevent costly inventory overstocking.
Traditionally, mastering the rate of stock replenishment was a challenge because it meant manually tracking every piece of stock as it moved along the supply chain via spreadsheets (or even a paper trail!). Today, however, automated stock replenishment is made possible by intelligent inventory management systems that monitor and update stock movements automatically, without the need for manual intervention. This equals significant time savings and reduces the risk of human error.
Stock replenishment principles
Safety stock
A key consideration for stock replenishment is safety stock . Also known as ‘buffer stock’, safety stock is stock held in a reserve to guard against shortages: maybe customers suddenly can’t get enough and you haven’t factored that into the demand, or maybe there’s a delay with the supplier. In any case, safety stock keeps you covered in the event of unforeseen circumstances.
Deciding how much safety stock to carry depends on a number of factors, such as lead times , demand, and carrying costs. Ultimately, you want to have enough safety stock to meet demand and support your usual stock replenishment cycle, but not so much that increased holding costs end up straining your finances.
Here’s a typical safety stock calculation:
- Multiply your maximum daily usage by your maximum lead time in days
- Multiply your average daily usage by your average lead time in days
- Calculate the difference between the two to determine your safety stock
Reorder point
Most inventory management systems follow replenishment rules to automate operations. Replenishment is typically triggered when inventory levels hit what’s known as the reorder point. The reorder point is the point at which stock needs to be reordered – taking into account current and future demand, along with how long it will take your supplier to send you the new order.
Calculating your reorder point manually takes three steps:
- Calculate your lead time demand in days.
- Calculate your safety stock in days
- Sum your lead time demand and your safety stock to determine your reorder point.
To make life easier, you can also use a reorder point calculator. It’ll let you know exactly when it’s time to place an order for a new shipment of products.
Using an inventory management system like QuickBooks Commerce, you can set a reorder point for different product variants to trigger stock replenishment automatically any time the reorder point is reached for a particular variant.
Knowing your reorder point and optimal safety stock level go hand in hand with maintaining good stock replenishment principles. However, most importantly, you should have a robust inventory management system in place that can automate the stock replenishment cycle – enabling you to not only maintain ideal stock levels but also quickly and easily shift with changing demand.