Sometimes, it feels like there aren’t enough hours in the day — scratch that, for many small businesses there aren’t. Oftentimes you’ll feel like you are constantly playing catch-up. You get one order away on deadlines when another comes in. And preparing for Black Friday, Cyber Monday or the Christmas rush? The less said about that the better! Spending more money to increase productivity seems like the only way out, but tight margins can make this difficult. But there is another way. You need to maximize your most valuable resource — time.
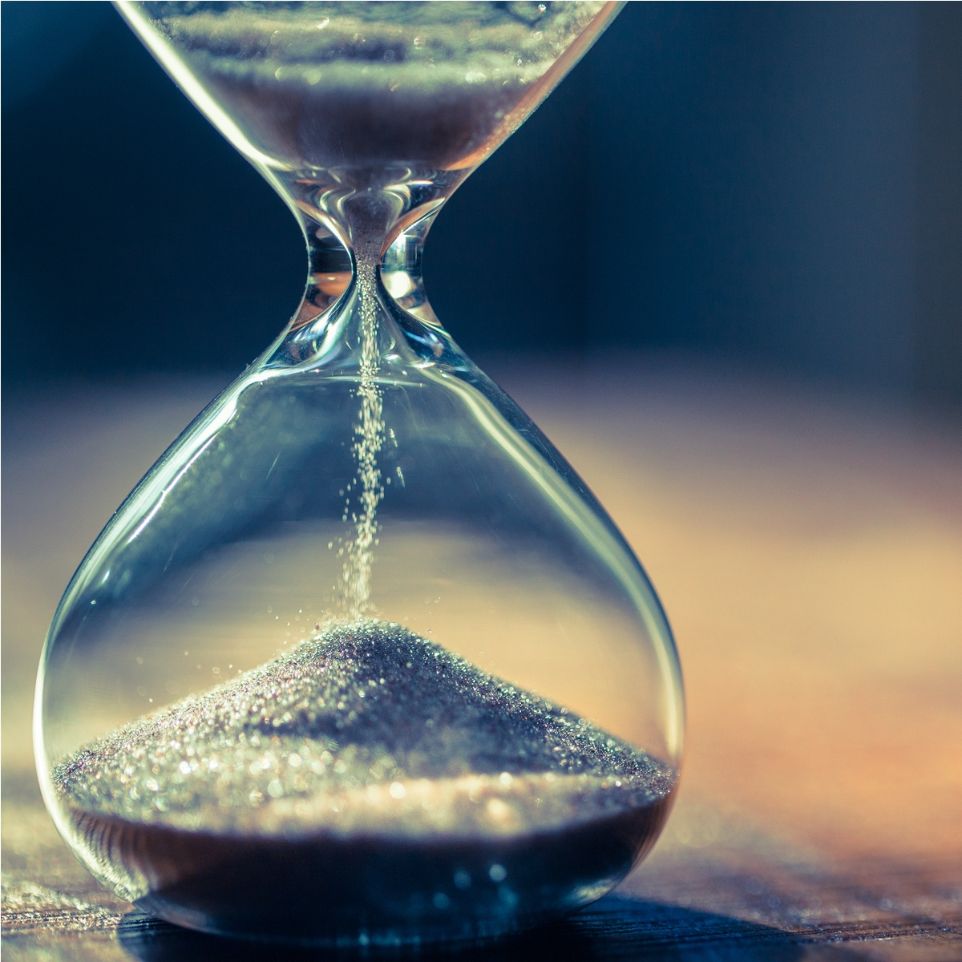
Master Production Schedule: How to grow your manufacturing business
Time is your most valuable asset
How you utilize every hour of every day plays a major role in your business success. Are you wasting time on repetitive or menial tasks? Rushing your work while trying to keep up and making mistakes, which results in more lost time? There's a good chance you are, and you’re not alone. Many business owners do several full-time jobs themselves, just to keep the lights on. They think that software solutions designed to streamline operations are only for large enterprises.
Your manufacturing output is a vital KPI that shows how efficient your overall order fulfillment process is. Good floor level control is one secret ingredient to maximizing this. Best of all, you don’t have to invest tons of money in new machinery, floor space, or staff to move the needle. Many small manufacturers can do more with what they already have with a few simple tweaks. We all have the same number of hours in the day, but how a business chooses to use its time determines how successful it can become.
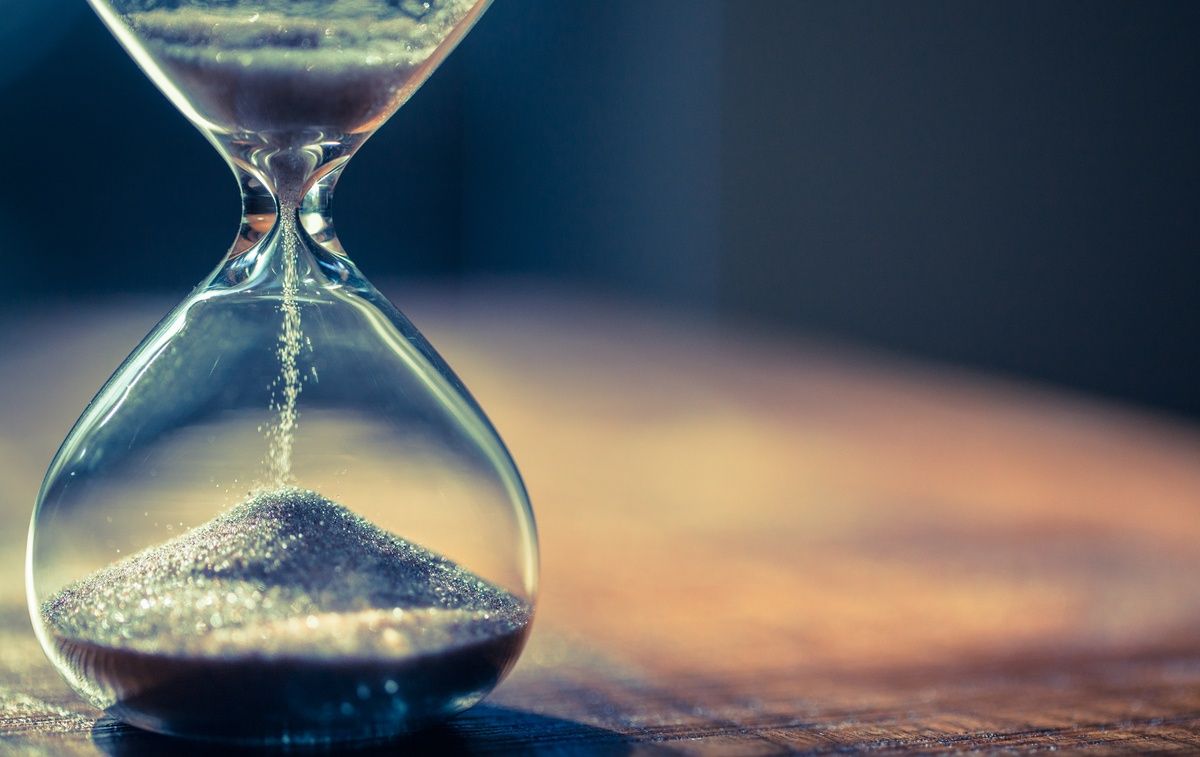
There seem to be 101 ways to measure time in manufacturing. Lead time, order fulfillment time, manufacturing cycle time, the list goes on. Obsessing over everything leads to information overload. Ignoring these vital metrics means your business could be underperforming without your knowledge.
As a product entrepreneur, you know there is no point starting a job without proper planning. But did you know there are industry-standard practices when it comes to production scheduling and planning? While putting them into practice may require you to invest time up front, they will pay dividends, saving countless hours in the long run.
The foundation is the Master Production Schedule (MPS). This is a rather scary sounding name for a document that contains information on every process in your business. The MPS may look different for every business. Designed correctly, it will include information on everything you make, including raw materials and operations.
What is Master Production Schedule (MPS)?
The MPS contains the Bill of Materials (BOM) for every product you manufacture. You should have a bill of materials for each product your manufacturing business produces. This is so you define the optimum way to produce your goods. This will prevent raw materials and time from being wasted as your staff know exactly what to do.
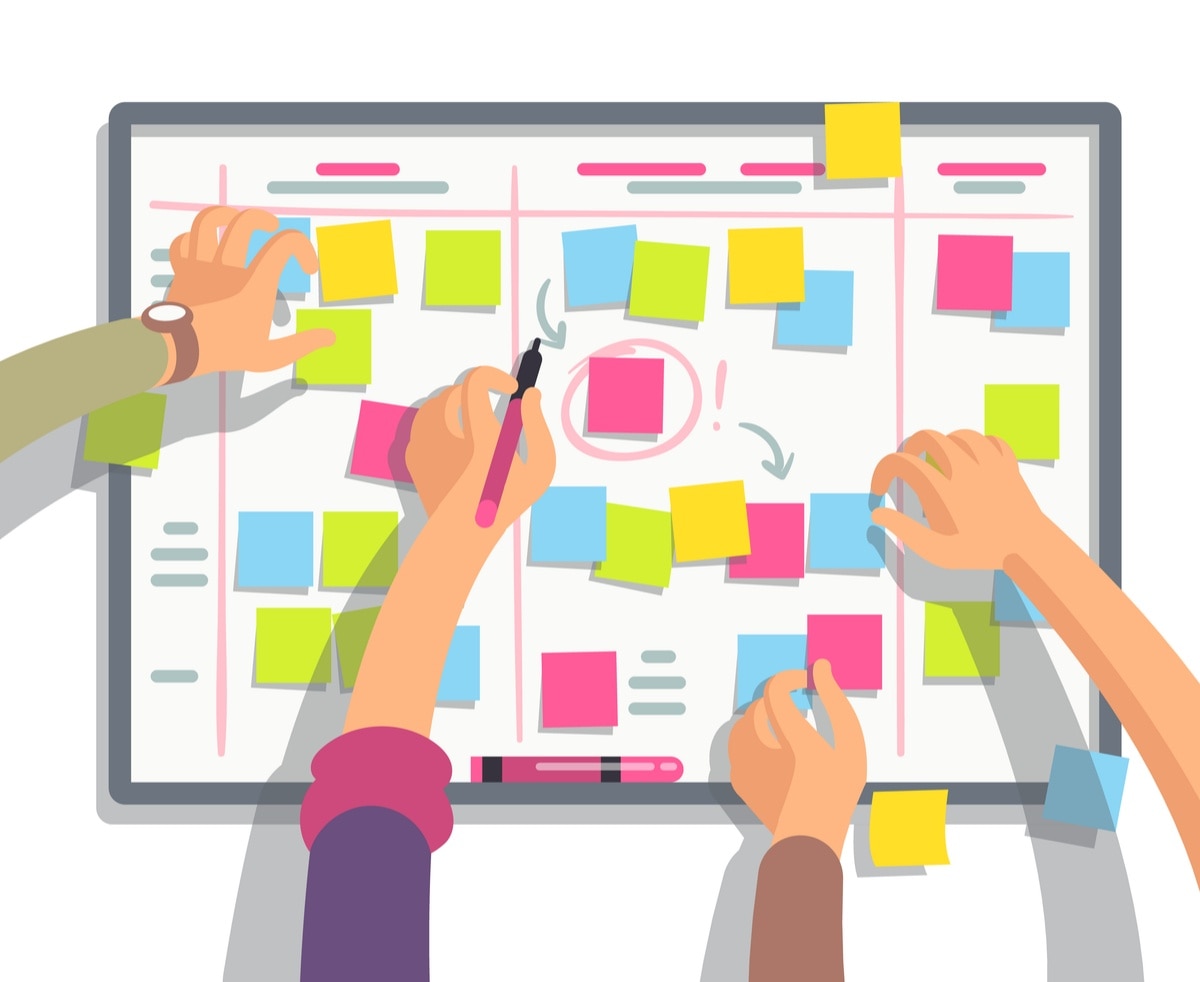
Every master production schedule tracks inventory, staffing, and production.
Mismanage one of these areas and it drags the whole system down. This is one of the biggest challenges facing small manufacturers - integrating each part of their business so it cohesively works together and optimizes time.
Believe it or not, many small business owners will get by without setting up a master production schedule. Of course you can get by, but as your business grows, cutting foundational corners like this will catch up with you and affect your ability to scale.
It’s easy to get overwhelmed with all the technical lingo and specialized knowledge. Many manufacturing businesses grew out of passion projects. In fact, most small business owners never went to business school. Suddenly having to deal with financial reports and a host of other tasks like managing inventory, accounting and orders from multiple sales channels will make you feel like a fish out of water.
When your business grows and you take on a few more employees, it’s easy to lose track of things. Perhaps you stay up late each night cutting down your backlog of tasks. You’re able stay on top of things, but it’s a struggle and this is when mistakes will mount and start to affect your bottom line.
Unclear task assignments can lead to unbalanced sub-assembly completion, unplanned bottlenecks and unscheduled downtime. All activity on your shop floor should be flowing smoothly from station to station, worker to worker.
If something is not working as it should, it not only causes your production to fall, but your staff morale to suffer. This will lead to lower motivation and lower performance levels. This is why floor level control is so important to customer satisfaction and growing your business.
How you deal with your orders directly affects your customers’ trust in you. Don’t underestimate the value of brand. Companies like Ikea spend decades building up a positive, recognizable brand. They are very careful how they present themselves to the world, as they know it could mean the difference between life and death for the business.
What if we told you that you can save many hours each week, without hiring anybody? What more could you do to grow your business? Don’t let the business of running your business take you away from what you love to do.
A match made in Heaven: QuickBooks Commerce + KatanaMRP
That’s where the QuickBooks Commerce & Katana integration comes in.
Together, QuickBooks Commerce and Katana MRP let manufacturers manage their entire multi-stage production process, workshop task assignments and master production schedule. The two systems sync seamlessly to handle complex manufacturing workflows, total inventory, or multichannel sales orders - Katana manages production and QuickBooks Commerce manages the rest, from order through to fulfillment.
The QuickBooks Commerce & Katana integration is your ultimate toolset for inventory, order and manufacturing management. It delivers a ready-made master production schedule right to your fingertips.
You can see your staff, materials, and operations in an easy-to-understand way. You can clearly see where every staff member should go and what they need to do. This makes task assignments clear and easy to understand, and you can do it from anywhere. Just assign tasks and your employees see real-time updates.
Keep track of all stock at all times. Know where everything goes. Ensure operations flows perfectly.
Get your floor level control back on track — crush your sales orders week in week out.